Metal manufacturing and custom machining solutions
Producing metal components using a specific method can enhance heat dissipation and increase thermal performance, improve the surface finish, allow for mass production of intricate designs, defend against corrosion, and give you different cost options.
The field of metal work is constantly evolving, with new materials and technology being used across a range of industries. We’re here to keep you at the forefront of design. When it comes to getting a part custom-made, our team of experts can explore the different choices available and offer you the most contemporary and practical solutions.
Discover the property benefits of different metalwork techniques and the endless possibilities for the manufacture of efficient heatsinks and metal enclosures. Accommodating low or high-volume customisations, we can hold stock for you, ready for you access within 48 hours and avoiding long lead times.
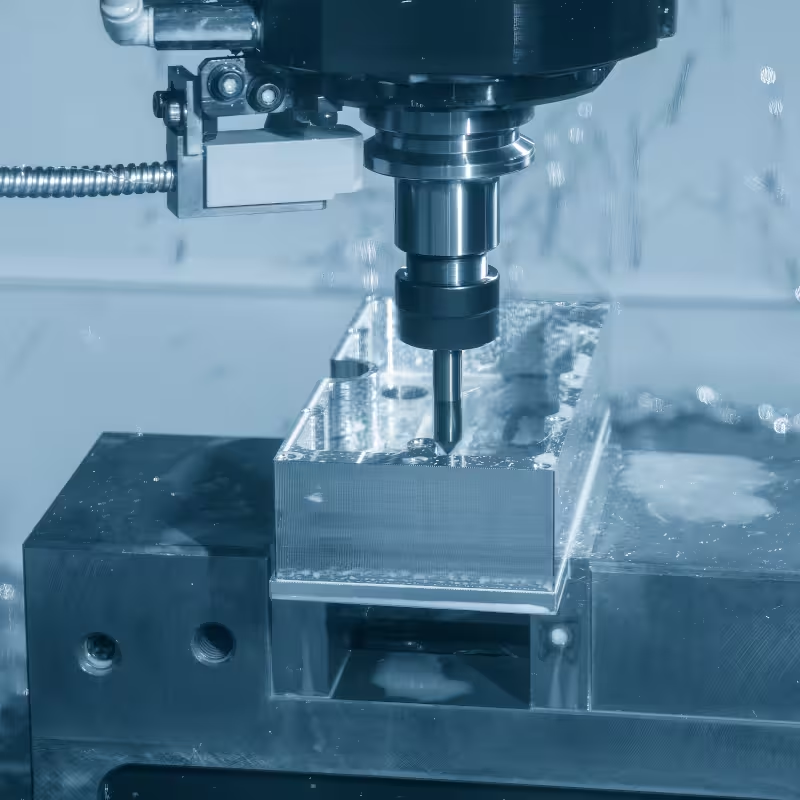
Extrusion
Most often used with aluminium and copper, extrusion forces metal through a shaped die (mould) which acts as a template and produces a continuous profile, ready for finishing with cutting, punching, or embossing. It’s great for producing intricate cross-sections and hollow shapes without any ridges that can be caused by seam welding and can be an extremely cost-effective solution. Metal extrusion is a good option for producing heatsinks and enclosures with precise tolerances and enhanced thermal conductivity.
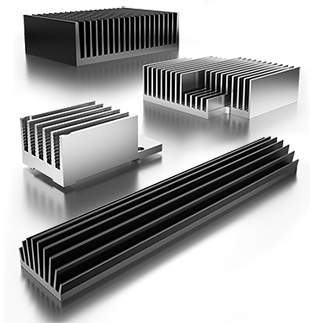
Skived
Through precise cutting or shaving, skiving can create intricate shapes with minimal material waste. Often used on aluminium, it’s an ideal method for precise detailing and efficient heat dissipation which is why it’s often used for heat sinks or copper sheets used for thermal management. The process can increase the surface area of the metal for better conductivity and create thin components made to tight tolerances which are essential in electronics.
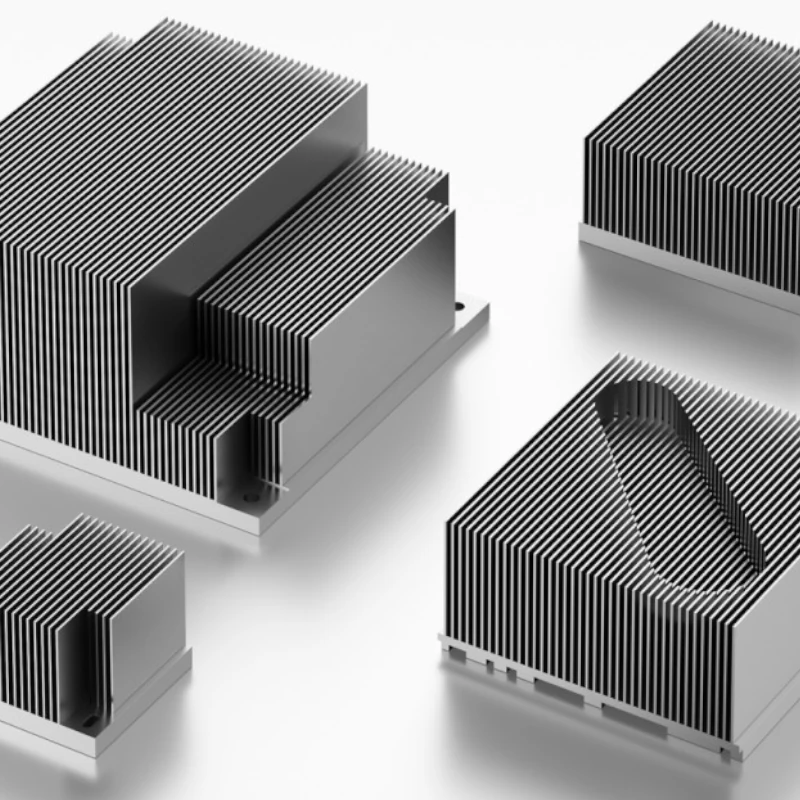
Die-cast
Die-casting is a highly versatile metalworking technique widely used for manufacturing electrical components, involving the injection of molten metals like aluminium, zinc, or magnesium into a mould cavity under high pressure. Die-casting offers the ability to create complex shapes with high accuracy, making it ideal for producing durable enclosures, connectors, and terminals with intricate designs. Die-casting is a cost-effective option for mass production and therefore a great choice for components in the automotive industry or consumer appliances.
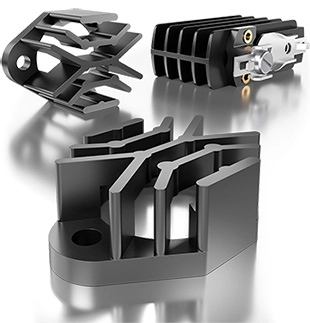
Epoxy Bonded
Epoxy resin is used to bond metal elements, creating a cohesive and insulated structure. It’s often used in the manufacture of lightweight components such as circuit boards, sensors, and connectors. Epoxy bonding provides electrical insulation, corrosion resistance, enhanced structural integrity and protection against environmental factors. It’s also extremely lightweight, making it suitable for applications where weight reduction is critical.
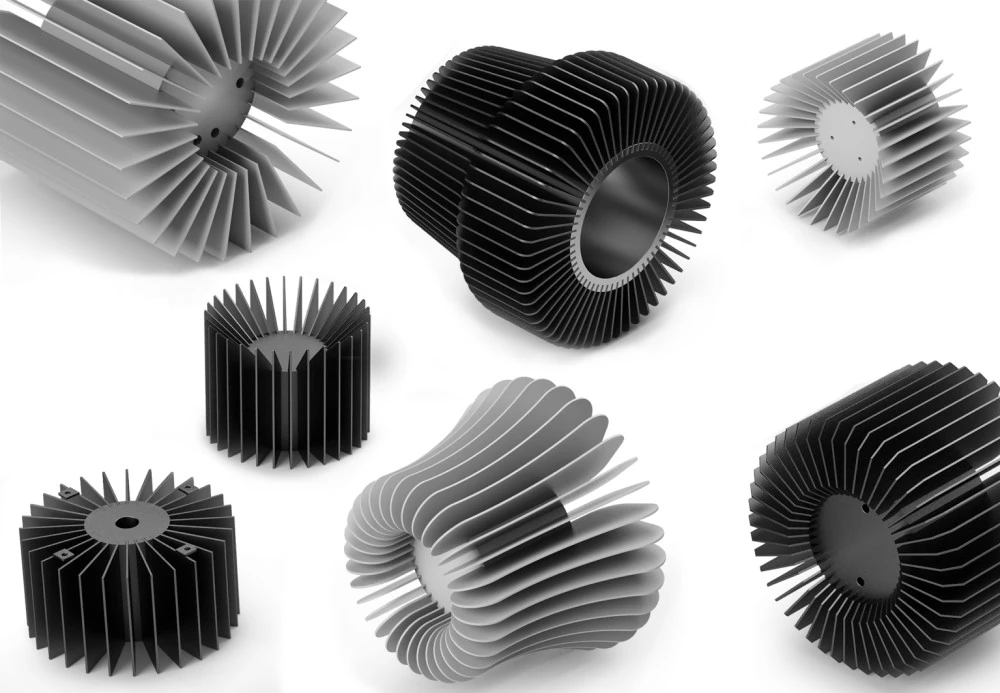
Press-Fin
The press-fin technique involves creating fin-like structures with precision pressing. This expands the surface area of the component and therefore enhances heat dissipation. It’s a process often used when manufacturing heatsinks for high power devices because of the improved cooling performance qualities, along with promoting lightweight designs, and cost-effective production. The finely pressed fins also provide structural strength, making press-fin components the perfect choice for maintaining optimal operating temperatures in a variety of electronic applications.
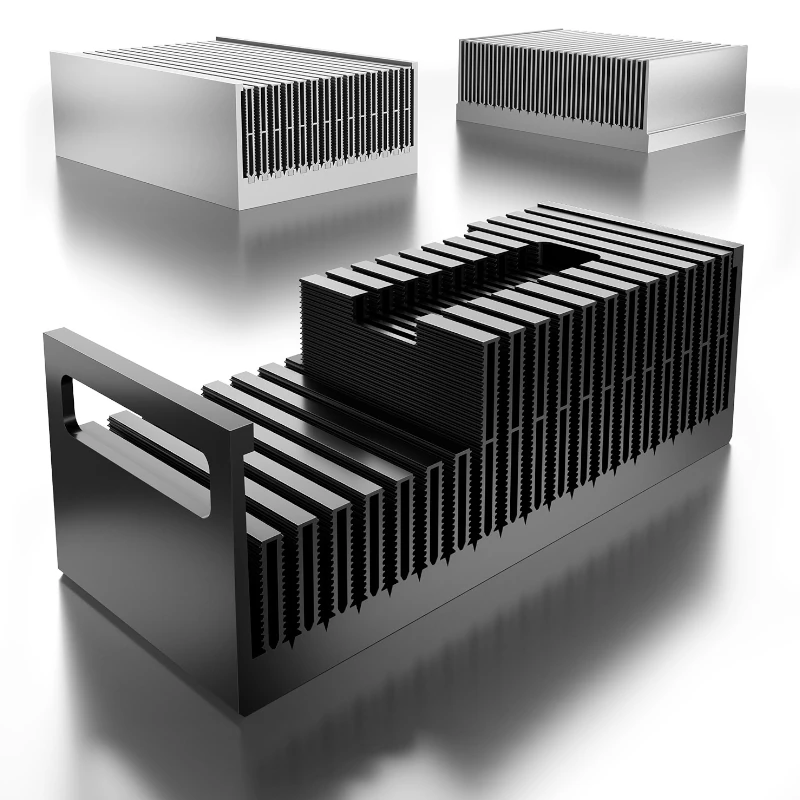
Stamped and Cold Forged
Stamping, which involves cutting or shaping metal sheets using a die (mould), is commonly used for manufacturing precise and uniform components such as connectors and contact points. Stamping is a cost-effective technique for mass production and offers high precision when creating intricate designs. On the other hand, forging, where metal is shaped through controlled deformation, provides superior strength and durability, which is ideal for critical components like electrical contacts and terminals.
Industries benefiting from both techniques include electronics, automotive, and aerospace, where stamped and forged parts contribute to the production of reliable and robust electrical systems with precise designs and enhanced mechanical properties.
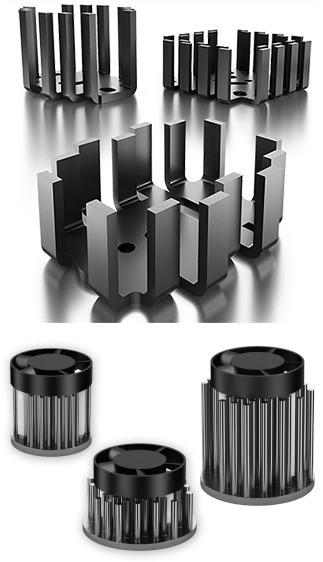
Metal Printing
Printed metal technology involves depositing metal layers onto a substrate using advanced printing techniques. This method is widely employed in the production of electronic components, such as printed circuit boards and sensors. Printed metal offers precise patterning, allowing for the creation of intricate circuits with high conductivity. This technique facilitates the production of lightweight and flexible electronic devices, making it suitable for applications in wearable technology and flexible displays. The versatility of printed metal also enhances the efficiency of the manufacturing process, making it a good choice for creating customised and complex electronic components with reduced material waste.
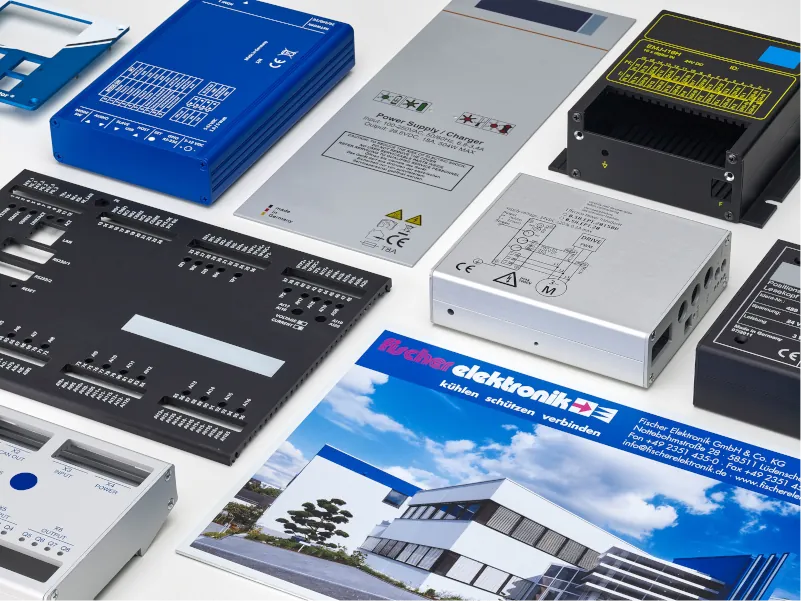
Finishes
Choosing the right finish is crucial in electronic component manufacturing. The right finish not only enhances product appearance but also influences its functionality. Finishes like anodising, plating, and powder coating are commonly employed to provide corrosion resistance, improve conductivity, and offer aesthetic appeal. Anodising creates a protective oxide layer on aluminium, enhancing its durability. Plating, on the other hand, improves conductivity and offers a polished appearance. Powder coating provides a durable and attractive finish, making it ideal for various electronic enclosures. Exploring the impact of different finishes is essential for achieving optimal performance and ensuring the longevity of electronic components in diverse applications.
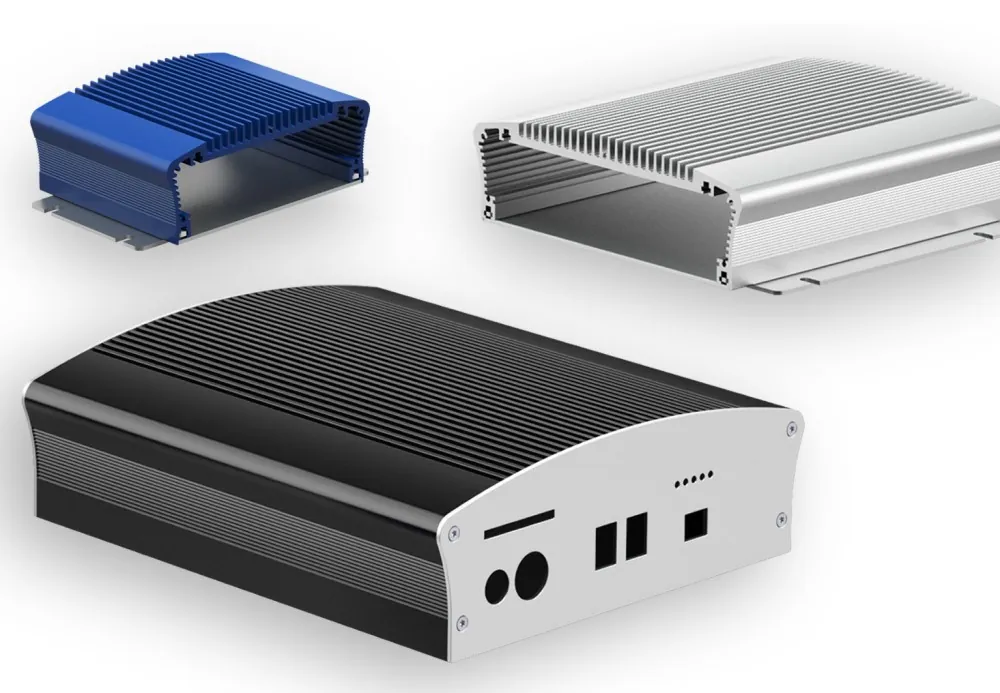
Off The Shelf Customisation
We have access to a large quantity of standard profiles that can be fully customised with the original manufacturer, eliminating the need for third-party machinists. This approach ensures quality control, reduces the risk of non-conformance, and cuts costs related to setup and shipping as well as accommodating both low and high-volume customisations. Additionally, DAU’s custom consigned stock allows for rapid delivery to the UK within 48 hours, giving you fast, reliable access to the components you need.
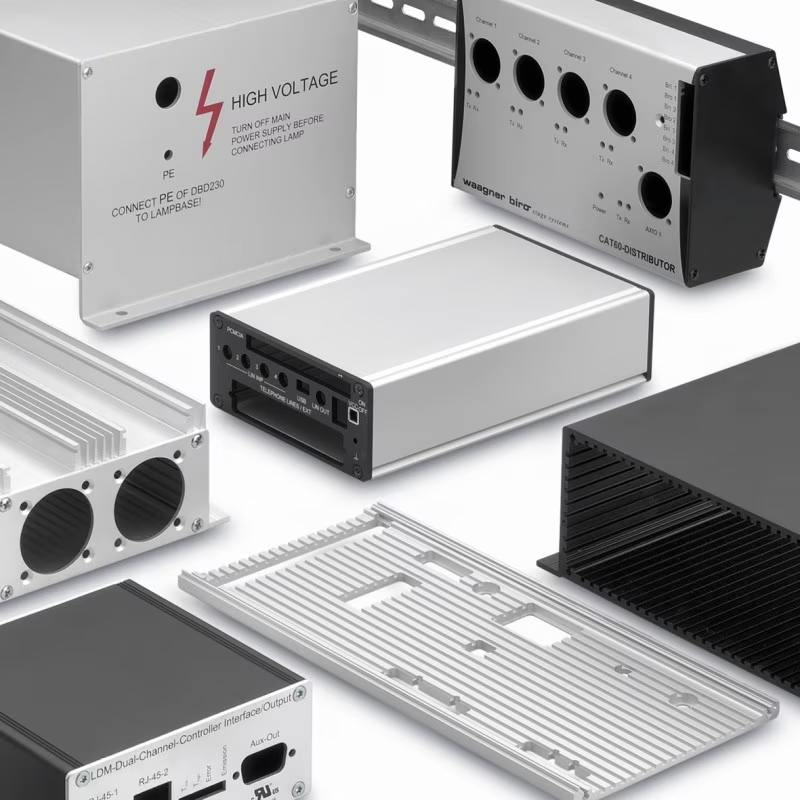
Customisation of metalwork (precision machining):
- 3,4 & 5 axis Precision CNC Machining inclusive of milling
- Multi-head drilling and tapping
Presswork:
- Punching
- Cut-outs
- Deburring saw cutting
- Cut-to-length
- Laser cutting
- Etching
Finishes:
- Clean & oil free
- Brushed
- Clear
- Coloured
- Black anodised (standard & hard – micron thickness tbc)
- Sand & bead blasting
- Visible parts (on show)
- Tumbling (for stamped heatsinks)
- Chromate conversion
Printing:
- Digital UV printing
- Silk screen printing
- Sub-elox printing
- Anodic printing
- Tampon printing
Water Cooled
Water-cooled heatsinks offer superior heat dissipation by using water to efficiently transfer heat away from high-performance components. They feature closed-loop systems, which are self-contained and require minimal maintenance, providing better cooling in a compact design. With less reliance on fans, these systems run quieter while delivering consistent, reliable performance, making them ideal for critical applications like servers and industrial electronics. Customisable designs cater to specific cooling needs, and durable, corrosion-resistant materials ensure long-lasting use. Overall, water-cooled heatsinks are an efficient, quiet, and reliable solution for advanced thermal management.
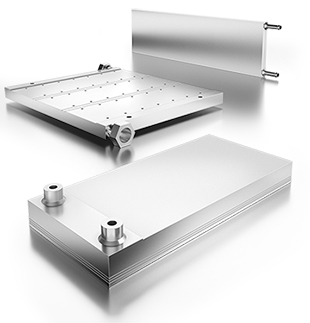